A System for High-Resolution Topology Optimization
Jun Wu, Christian Dick, Rüdiger Westermann
Computer Graphics and Visualization Group, Technische Universität München, Germany

Abstract
A key requirement in 3D fabrication is to generate objects with individual exterior shapes and their interior being optimized to application-specific force constraints and low material consumption. Accomplishing this task is challenging on desktop computers, due to the extreme model resolutions that are required to accurately predict the physical shape properties, requiring memory and computational capacities going beyond what is currently available. Moreover, fabrication-specific constraints need to be considered to enable printability. To address these challenges, we present a scalable system for generating 3D objects using topology optimization, which allows to efficiently evolve the topology of high-resolution solids towards printable and light-weight-high-resistance structures. To achieve this, the system is equipped with a high-performance GPU solver which can efficiently handle models comprising several millions of elements. A minimum thickness constraint is built into the optimization process to automatically enforce printability of the resulting shapes. We further shed light on the question how to incorporate geometric shape constraints, such as symmetry and pattern repetition, in the optimization process. We analyze the performance of the system and demonstrate its potential by a variety of different shapes such as interior structures within closed surfaces, exposed support structures, and surface models.
Keywords: Topology optimization, 3D printing, finite element analysis, multigrid, GPU
Associated publications
A System for High-Resolution Topology Optimization
Jun Wu, Christian Dick, Rüdiger Westermann
IEEE Transactions on Visualization and Computer Graphics [Preprint][Bibtex]
3D printed shapes
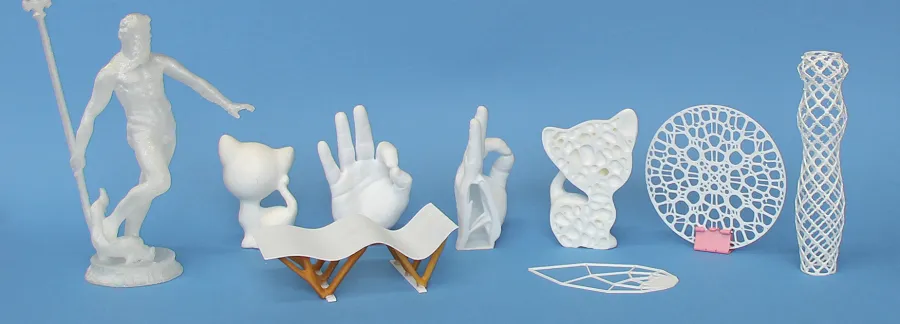
Demo
An executable demo will be available soon. Please contact Dr. Jun Wu